The 9 Different Types of 3D Printers
3D printing is the latest thing to excite anyone who loves easy-to-use interactive technology. Engineers and scientists have actually been working with this amazing equipment since way back in 1983. That’s the time when an American engineer named Charles (Chuck) Hull invented the first ever 3D printer. He called it his SLA machine, which stands for stereolithography apparatus.
Some in the industry refer to part of the 3D printing process as Additive Manufacturing (AM), but we’ll use its practical name here—3D Printing. This will keep the guide consistent and easy to read.
The Reasons for Several Types of 3D Printer
The reasons there are different types of 3D printers and printing processes are similar to that of the 2D printers we’re so familiar with. It all comes down to the following six considerations:
- Printer cost
- Print quality
- Print speed
- Printer capability
- Practicality
- User expectations
Some printers only print text—others text and graphics. The technologies and materials used also vary, and the way the machine extrudes ink to paper. 3D printers are even smarter. And like their 2D counterparts, they also offer a range of options including quality, materials, and price.
The 3D Printing Process in a Nutshell
The 3D printing process is no longer difficult for the home user once you grasp the basic principles. OK, so printers, printing materials, printed objects, and 3D printing software can all vary. Yet despite this, the process from design to end product follows a similar path. We’ve covered these processes in some detail in another guide, but here’s how it looks in a nutshell:
- User has access to a 3D modeling application or a 3D scanner
- User creates a virtual design (3D model) of the object they want to print in 3D
- User typically saves their design as a Computer Aided Design file, or CAD for short
- User slices their CAD file before sending it to the printer
- User uploads the sliced CAD file to the 3D printer
- Printer reads each slice in the 2D file to create the three dimensional object
Who Is this Guide For?
This simple guide is for those who want to understand the differences between different 3D printing types. It’s also for hobbyists, schools, libraries, and anyone else who wants to invest in this amazing technology. If you know nothing at all about 3D printing—but would like to learn—this guide is for YOU. Don’t worry, we’re not going to overwhelm you or blind you with science.
By the end of this guide, you’ll have a good, basic understanding of all the 3D printer types available today. If you’re thinking about investing in a 3D printer, we’ve got you covered. You’re going to be in a much better position to make a well-informed decision before parting with your hard earned cash.
The Focus of this Guide
This guide focuses on the most common types of 3D printers in use today. We’ll introduce each of these machines by their long names first. After that we’ll use the appropriate acronyms to keep the reading easy. For example, stereolithography becomes SLA. And Laminated Object Manufacturing becomes LOM, as two examples.
Here are the nine 3D printer types you will learn about:
- Stereolithography (SLA)
- Digital Light Processing (DLP)
- Fused deposition Modeling (FDM)
- Selective Laser Sintering (SLS)
- Selective Laser Melting (SLM)
- Electronic Beam Melting (EBM)
- Laminated Object Manufacturing (LOM)
- Binder Jetting (BJ)
- Material Jetting (MJ)
The Basic Components of a 3D Printer
Before we begin to look at the various 3D printer types and printing practices, we’ll take a moment to list the main components of these machines. There are many parts, and each one plays a crucial role in the printing process. We’re not going to get too technical here. It’s still important, however, to know what the main components are. This will help you to better understand the printing processes as you read through the various sections.
The main components, and their use, in a 3D printer are:
- 3D Printer Frame: Holds the machine together
- 3D Printer Head movement mechanics: moves relative to the print bed in all directions
- 3D Printer Head: Nozzle that deposits filament or applies colors and liquid binder
- 3D Build Platform or Build Bed: The part of the printer where the object is printed
- 3D Printer Stepper Motors (at least 4): Used for precise positioning and speed control
- 3D Printer Electronics: Used to drive motors, heat the extruder and much more
- 3D Printer Firmware: Permanent software used to control every aspect of a 3D printer
- 3D Printer Software: Not part of the actual printer but still needed for the printing process
You can read a more in-depth explanation of the 3D printer components here.
3D Support Substances
Many 3D printers use various substances that support complex geometries. Support materials are as essential to the 3D printing process as the actual base materials. Without support during the build there would not be a successful outcome. These materials offer a better solution than the old physical support structures of the past. Once printing is complete, the user simply removes any support substance from the finished part.
Some 3D technologies use support materials that dissolve when placed into a chemical bath. Others will use the surrounding powder as a way to keep everything in place. And there are those which use a squidgy, gel-like substance. You will read about which printing process uses what kind of support materials in this guide.
1) Stereolithography (SLA) Technology
SLA is a fast prototyping process. Those who use this technology are serious about accuracy and precision. It can produce objects from 3D CAD data (computer-generated) files in just a few hours. This is a 3D printing process that’s popular for its fine details and exactness. Machines that use this technology produce unique models, patterns, prototypes, and various production parts. They do this by converting liquid photopolymers (a special type of plastic) into solid 3D objects, one layer at a time. The plastic is first heated to turn it into a semi-liquid form, and then it hardens on contact. The printer constructs each of these layers using an ultra violet laser, directed by X and Y scanning mirrors. Just before each print cycle, a recoater blade moves across the surface to ensure each thin layer of resin spreads evenly across the object. The print cycle continues in this way, building 3D objects from the bottom up.
Once completed, someone takes the 3D object from the printer and detaches it carefully from the platform. The 3D part will usually have a chemical bath to remove any excess resin. It’s also common practice to post-cure the object in an ultra violet oven. What this does is render the finished item stronger and more stable. Depending on the part, it may then go through a hand sanding process and have some professional painting done. SLA printing has become a favored economical choice for a wide variety of industries. Some of these include automotive, medical, aerospace, entertainment, and also to create various consumer products.
Don’t Miss: Best SLA/DLP Printers
Some SLA printers include: 3D printer Pegasus Touch SLA technology, XYZprinting Nobel 1.0 SLA 3D Printer, SUNLU SLA Desktop 3D Printer, Form 1+ SLA 3D Printer.
2) Digital Light Processing (DLP) Technology
DLP is the oldest of the 3D printing technologies, created by a man called Larry Hornbeck back in 1987. It’s similar to SLA (see above), given that it also works with photopolymers. The liquid plastic resin used by the printer goes into a translucent resin container. There is, however, one major difference between the two, which is the source of light. While SLA uses ultra violet light, DLP uses a more traditional light source, usually arc lamps. This process results in pretty impressive printing speeds. When there’s plenty of light, the resin is quick to harden (we’re talking seconds). Compared to SLA 3D printing, DLP achieves quicker print times for most parts. The reason it’s faster is because it exposes entire layers at once. With SLA printing, a laser has to draw out each of these layers, and this takes time.
Another plus point for DLP printing technology is that it is robust and produces high resolution models every time. It’s also economical with the ability to use cheaper materials for even complex and detailed objects. This is something that not only reduces waste, but also keeps printing costs low.
Don’t Miss: Best SLA/DLP Printers
Some DLP printers include: Makex M-one Desktop DLP 3d Printer, Desktop UV DLP, LumiPocket – Miniature DLP, Solus DLP 3D Printer
3) Fused Deposition Modeling (FDM) Technology
FDM is a 3D printing process developed by Scott Crump, and then implemented by Stratasys Ltd., in the 1980s. It uses production grade thermal plastic materials to print its 3D objects. It’s popular for producing functional prototypes, concept models, and manufacturing aids. It’s a technology that can create accurate details and boasts an exceptional strength to weight ratio.
Before the FDM printing process begins, the user has to slice the 3D CAD data (the 3D model) into multiple layers using special software. The sliced CAD data goes to the printer which then builds the object layer at a time on the build platform. It does this simply by heating and then extruding the thermoplastic filament through the nozzle and onto the base. The printer can also extrude various support materials as well as the thermoplastic. For example, as a way to support upper layers, the printer can add special support material underneath, which then dissolves after the printing process. As with all 3D printers, the time it takes to print all depends on the objects size and its complexity.
Like many other 3D technologies, the finished object needs cleaning. Raw FDM parts can show fairly visible layer-lines on some objects. These will obviously need hand sanding and finishing after printing. This is the only way to get a smooth, end product with an even surface. FDM finished objects are both functional and durable. This makes it a popular process for use in a wide range of industries, including for mechanical engineering and parts manufacturers. BMW uses FDM 3D printing, as does the well-known food company Nestle, to name just a couple.
Don’t Miss: Best FDM Printers
Some FDM printers include: JGAURORA 3d Desktop FDM Printer, ALUNAR High Resolution Desktop FDM 3D Printer, Original Prusa i3 MK2, PowerSpec 3D Pro, Lulzbot Mini, FlashForge Creator Pro.
4) Selective Laser Sintering (SLS) Technology
An American businessman, inventor, and teacher named Dr. Carl Deckard developed and patented SLS technology in the mid-1980s. It’s a 3D printing technique that uses high power CO2 lasers to fuse particles together. The laser sinters powdered metal materials (though it can utilize other materials too, like white nylon powder, ceramics and even glass). Here’s how it works:
The build platform, or bed, lowers incrementally with each successive laser scan. It’s a process that repeats one layer at a time until it reaches the object’s height. There is un-sintered support from other powders during the build process that surround and protect the model. This means the 3D objects don’t need other support structures during the build. Someone will remove the un-sintered powders manually after printing. SLS produces durable, high precision parts, and it can use a wide range of materials. It’s a perfect technology for fully-functional, end-use parts and prototypes. SLS is quite similar to SLA technology with regards to speed and quality. The main difference is with the materials, as SLS uses powdered substances, whereas SLA uses liquid resins. It’s this wide variety of available materials that makes SLA technology so popular for printing customized objects.
Some SLA printers include: XYZprinting Nobel 1.0 SLA 3D Printer, SUNLU SLA Desktop 3D Printer, Formlabs Form 2, 3D Systems ProJet 1200, DWS Lab Xfab.
5) Selective Laser Melting (SLM) Technology
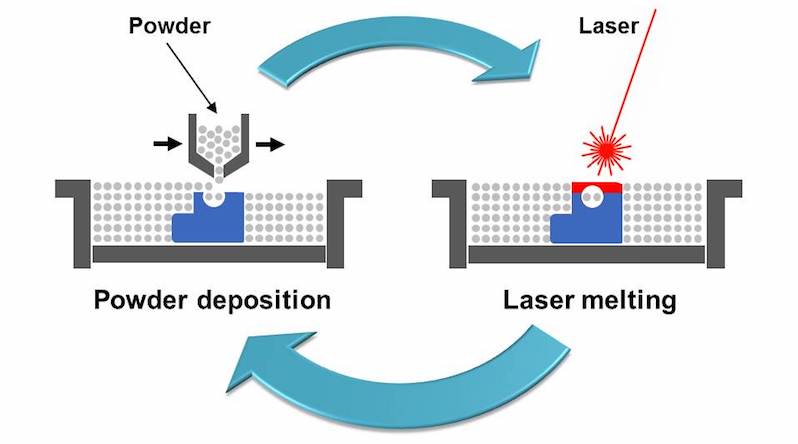
SLM made its debut appearance back in 1995. It was part of a German research project at the Fraunhofer Institute ILT, located in the country’s most western city of Aachen. Like SLA (see above), SLM also uses a high-powered laser beam to form 3D parts. During the printing process, the laser beam melts and fuses various metallic powders together. The simple way to look at this is to break down the basic process like thus:
Powdered material + heat + precision + layered structure = a perfect 3D object.
As the laser beam hits a thin layer of the material, it selectively joins or welds the particles together. After one complete print cycle, the printer adds a new layer of powered material to the previous one. The object then lowers by the precise amount of the thickness of a single layer. When the print process is complete, someone will manually remove the unused powder from the object. The main difference between SLM and SLS is that SLM completely melts the powder, whereas SLS only partly melts it (sinters). In general, SLM end products tend to be stronger as they have fewer or no voids.
A common use for SLM printing is with 3D parts that have complex structures, geometries and thin walls. The aerospace industry uses SLM 3D printing in some of its pioneering projects. These are typically those which focus on precise, durable, lightweight parts. It’s a costly technology, though, and so not practical or popular with home users for that reason. SLM is quite widespread now among the aerospace and medical orthopedics industries. Those who invest in SLM 3D printers include researchers, universities, and metal powder developers. There are others too, who are keen to explore the full range and future potential of metal additive manufacturing in particular.
Some SLM industrial printers include: SLM Solutions SLM 125, 280, and 500, Realizer SLM 125, Optomec LENS 450, others.
6) Electron Beam Melting (EBM) Technology
A Swedish company called Arcam AB founded EBM® in 1997. This is a 3D printing technology similar to SLM (see above), in that it uses a powder bed fusion technique. The difference between the two is the power source. The SLM approach above uses high-powered laser in a chamber of noble, or inert gas. EBM, on the other hand, uses a powerful electron beam in a vacuum. Aside from the power source, the remaining processes between the two are quite similar. EBM’s main use is to 3D print metal parts. Its main characteristics are its ability to achieve complex geometries with freedom of design. EBM also produces parts that are incredibly strong and dense in their makeup.
Here are a few of EBM’s other impressive features:
- Doesn’t need extra auxiliary equipment for the 3D printing process
- Has increased efficiency using raw materials
- Lessens lead times resulting in parts getting to market faster
- Can create fully functional, durable parts on demand for wide-ranging industries
The printing process starts like most others in that the user has to first create a 3D model, or computer-generated digital file.
An industrial EBM printer includes: Arcam Q20
7) Laminated Object Manufacturing (LOM) Technology
A Californian company called Helisys Inc. (now Cubic Technologies), first developed LOM as an effective and affordable method of 3D printing. A US design engineer called Michael Feygin—a pioneer in 3D printed technologies—originally patented LOM.
LOM is a rapid prototyping system that works by fusing or laminating layers of plastic or paper using both heat and pressure. A computer-controlled blade or laser cuts the object to the desired shape. Once each printed layer is complete, the platform moves down by about 1/16th of an inch, ready for the next layer. The printer then pulls a new sheet of material across the substrate where it’s adhered by a heated roller. This basic process continues over and over until the 3D part is complete.
According to Wikipedia, the LOM printing works as follows:
- Sheet is adhered to a substrate with a heated roller.
- Laser traces desired dimensions of prototype.
- Laser cross hatches non-part area to facilitate waste removal.
- Platform with completed layer moves down out of the way.
- Fresh sheet of material is rolled into position.
- Platform downs into new position to receive next layer.
- The process is repeated.
It might not be the most popular method of 3D printing today, but LOM remains one of the fastest nonetheless. It’s also perhaps the most affordable method for creating 3D prototypes. The reason for this is because of the low cost of materials used (papers and plastics). It’s also a process that can create fairly large 3D printed objects. Those who continue to use LOM printers today include architects, artists, and product developers.
One popular LOM printer is: The Mcor Matrix
8) Binder Jetting (BJ) Technology
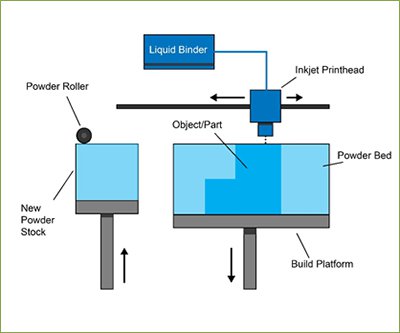
The Massachusetts Institute of Technology (MIT) first invented BJ 3D printing. You may also hear this technology referred to in other names, including:
- Powder bed printing
- Inkjet 3D printing
- Drop-on-powder
- Binder jetting (BJ). This is the most popular name and the one we’ll use to refer to it.
BJ is a 3D printing process that uses two types of materials to build objects: a powder-based material (usually gypsum) and a bonding agent. As the name suggests, the “bonding” agent acts as a strong adhesive to attach (bond) the powder layers together. The printer nozzles extrude the binder in liquid form similar to a regular 2D inkjet printer. After completing each layer, the build plate lowers slightly to allow for the next one. This process repeats until the object reaches its required height.
The four popular materials used in BJ printing include:
- Ceramics
- Metals
- Sand
- Plastics
It’s not possible to get super high-resolution or overly rugged 3D objects with BJ printing, but there are other advantages. For example, these printers allow you to print parts in full color. To do this, you simply add color pigments to the binder, which typically include black, white, cyan, yellow, and magenta. This technology is still advancing, so expect more great things to come in the future. At the time of writing, some applications of BJ 3D printing include rapid prototyping, and various uses in the aerospace, automotive, and medical industries.
Some BJ printers include: Addwii Unveils The X1, ExOne R2, ZCorp Spectrum z510
9) Material Jetting (MJ) Polyjet and Wax Casting Technology
You will also hear Material Jetting referred to as wax casting. Unlike other 3D printing technologies, there isn’t a single inventor for MJ. In fact, up until recent times it’s been more of a technique than an actual printing process. It’s something jewelers have used for centuries. Wax casting has been a traditional process where the user produces high-quality, customizable jewelry. The reason it gets a mention here is because of the introduction of 3D printing. Thanks to the arrival of this technology, wax casting is now an automated process. Today, MJ 3D printers produce high-resolution parts, mainly for the dental and Jewelry industries,
For jewelers who want to experiment with various casts—as most jewelers do—MJ is now their leading 3D technology. At the time of writing, there are a few high-quality professional wax 3D printers on the market. Here’s how they work:
Once the 3D model (CAD file) is uploaded to the printer, it’s all systems go. The printer adds molten (heated) wax to the aluminum build platform in controlled layers. It achieves this using nozzles that sweep evenly across the build area. As soon as the heated material lands on the build plate it begins to cool down and solidify (UV light helps to cure the layers). As the 3D part builds up, a gel-like material helps to support the printing process of more complex geometries. Like all support materials in 3D printing, it’s easy to remove it afterward, either by hand or by using powerful water jets. Once the part is complete you can use it right away, no further post-curing necessary.
There are also Polyjet MJ 3D printers, which use photopolymer-resins rather than synthetic waxes. Polyjet technology also offers very good resolution. Unlike digital wax printers, people use Polyjet devices to create parts for a wide range of industries.
Some MJ printers include: ABS 3D printer, PLA 3D printer (large format), HP Multi Jet Fusion
Summing Up
3D printers and print technology is advancing all the time. As it does, prices will continue to fall as the devices and processes become ever more impressive. If you’ve read this guide from top to bottom, you will now have a good basic understanding of the different 3D printers and how they work. You will also know of the various materials printers use and the industries they support. And if you need a refresher, you can simply revisit any section of this guide at any time.
No Printer No Problem
Remember too, you don’t have to own a 3D printer to learn the technology or to print in 3D. There are plenty of free web-based 3D printing design & modeling software programs to choose from. Once you have your 3D design, you are good to go. You should be able to find someone in your local area with a 3D printer who will print your project for a nominal fee. Check out the schools, libraries or small startups at local co-working centers. Failing that, submit your 3D digital file online and let one of the 3D services print your model.