Silent Underwater Propulsion Inspired By Octopus’s And Built By 3D Printers
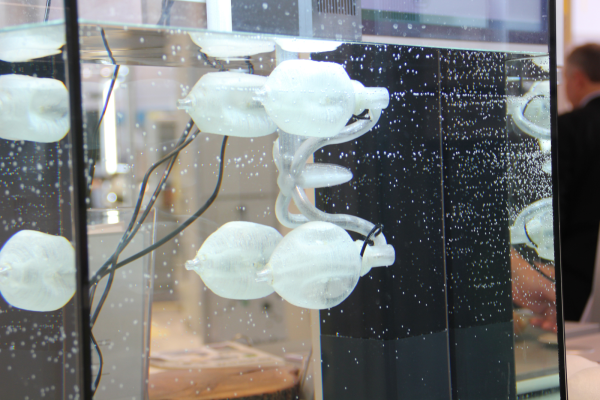
Nature’s bizarre way of doing things can sometimes be the best answer to engineering problems and Researchers at the Fraunhofer Institute for Manufacturing Engineering and Automation have come to the same conclusion. They have developed a silent underwater propulsion system that takes a leaf out of octopus’s books.
One of the many ways that the octopus’s and squid can move about in their watery homeland is via water jet propulsion. Even though the sea creatures make water jet propulsion look easy, researchers at Fraunhofer have been scratching their heads over the complicated process. They then decided to turn to 3D printing to allow them to make complicated parts that typical manufacturing techniques can’t do. The octopod-inspired propulsion system consists of four bulbs made from a flexible plastic polymer. Water is then sucked into each bulb with an actuator. A recirculation valve is used to keep water from flowing back out the bulb, whereas an octopus uses its muscles. A hydrolic piston is then used to expel the water at a greater force.
Andreas Fischer, an engineer at IPA in Stuttgart said “Squids use this type of movement mainly if they are trying to flee suddenly and quickly. The system is simple, but effective. When they use it, the octopods can speed up considerably over short distances.”
Fischer then goes on to say “Our underwater actuator is well-suited for maneuvering small boats. It can also be used as a floating aid for water sport devices such as jet skis, surf boards, or scooters that pull divers into deep water. In contrast to ship propellers, it is quiet, and fish cannot get caught in it.”
Researchers turned to 3D printing for an efficient way to produce the components that would make up the propulsion system. Everything apart from the hydraulic piston is built by the 3D printer and can even be printed in a single step. They used standard fused deposition modelling for the printing technique. This is where a thermoplastic is heated and then extruded out in layers to create a 3D object. Fischer used polyurethane for the design because it allowed for a propulsion system that is both flexible and strong.
Apparently the researchers can scale the system to allow for much larger or smaller components. “At the moment, the maximum construction volume of FDM facilities is 91.4 x 61 x 91.4 cm, whereby no more than ten different thermoplastics can be processed in layers. By integrating continuous filament into thermoplastics, for example, we can manufacture carbon fiber-reinforced components quickly and at a low cost,” says Fischer.
Fischer and his team see this technology powering small boats and various types of watercraft. He also hopes that larger versions could be made for enormous ships. The main limiting factor for this would be the size of the 3D printer. Components could also be replaced easier due to the nature of 3D printing.
Here’s a video of an Indonesian Mimic Octopus moving about to get the idea.